高产之下怎样高效轻松干活?进东风工厂看一看!
技术升级、精益改善、智能制造吗,在高产战车呼啸驰骋的当下, 东风商用车 正在用更“智慧”的方式, 降低劳动强度、优化工作环境, 提高生产效率、壮大制造实力
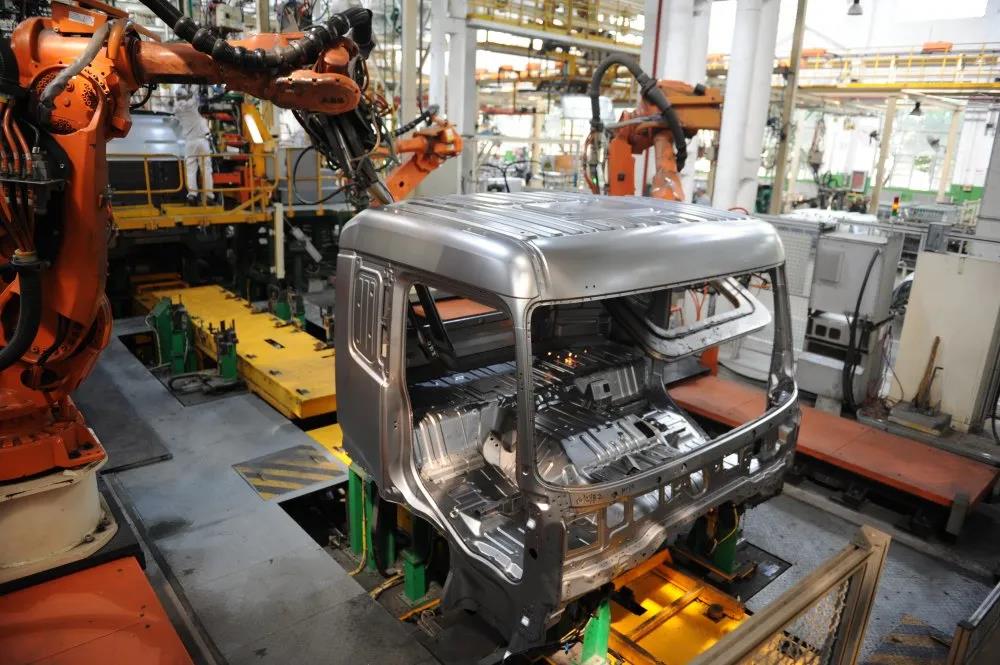
智能制造
随着时代发展,汽车制造技术日新月异,智能制造已成为当前主流发展方向。在东风商用车车身厂看来,未来的工厂一定是智能制造的工厂,这不是追求“高大上”,而是要立足实际、实现价值、创造财富。
自去年10月正式启动智能制造工作以来,车身厂制定了智能制造分阶段目标和初步规划,组建了数字化工艺管理平台团队、全面质量管理体系团队、智能生产物流管理系统团队、设备管理和预警系统团队及智能制造大数据中心团队。
如今,车身厂智能制造总体框架更为清晰,各个子项、子系统的规划逐步细化,有些新技术应用已形成课题并展开,进一步提高生产效率、降低员工劳动强度。
下阶段,工厂智能制造工作方向将从以学习研究为主转为以实施应用研究为主。
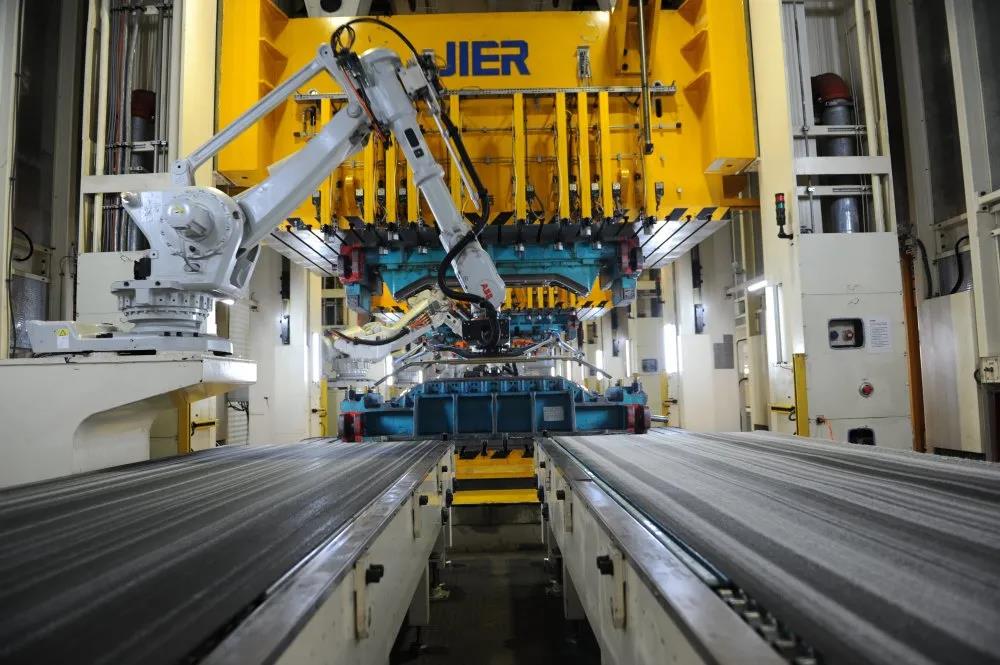
未来,车身厂将做到“两个结合”,一是结合东风商用车下一代新品的投入,二是要结合工厂改扩建和新项目建设,将学习研究的成果转化为可行性课题推进实施,打造智能、绿色、环保、国内领先的智能工厂。
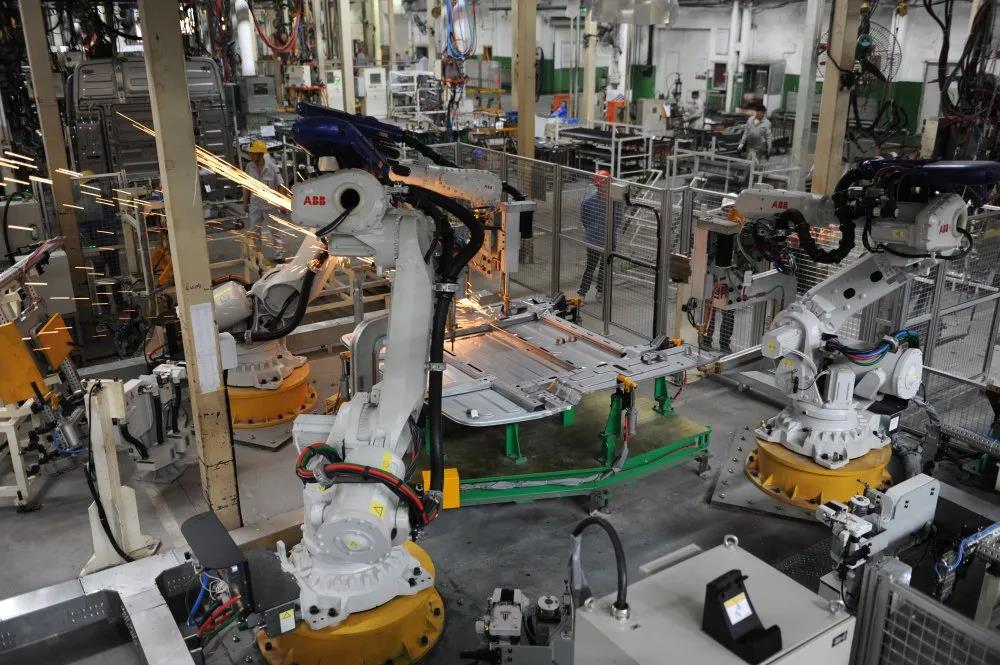
装备升级
5月,东风锻造有限公司锻造厂的一台自动喷墨润滑机成了该厂的“高产重器”。
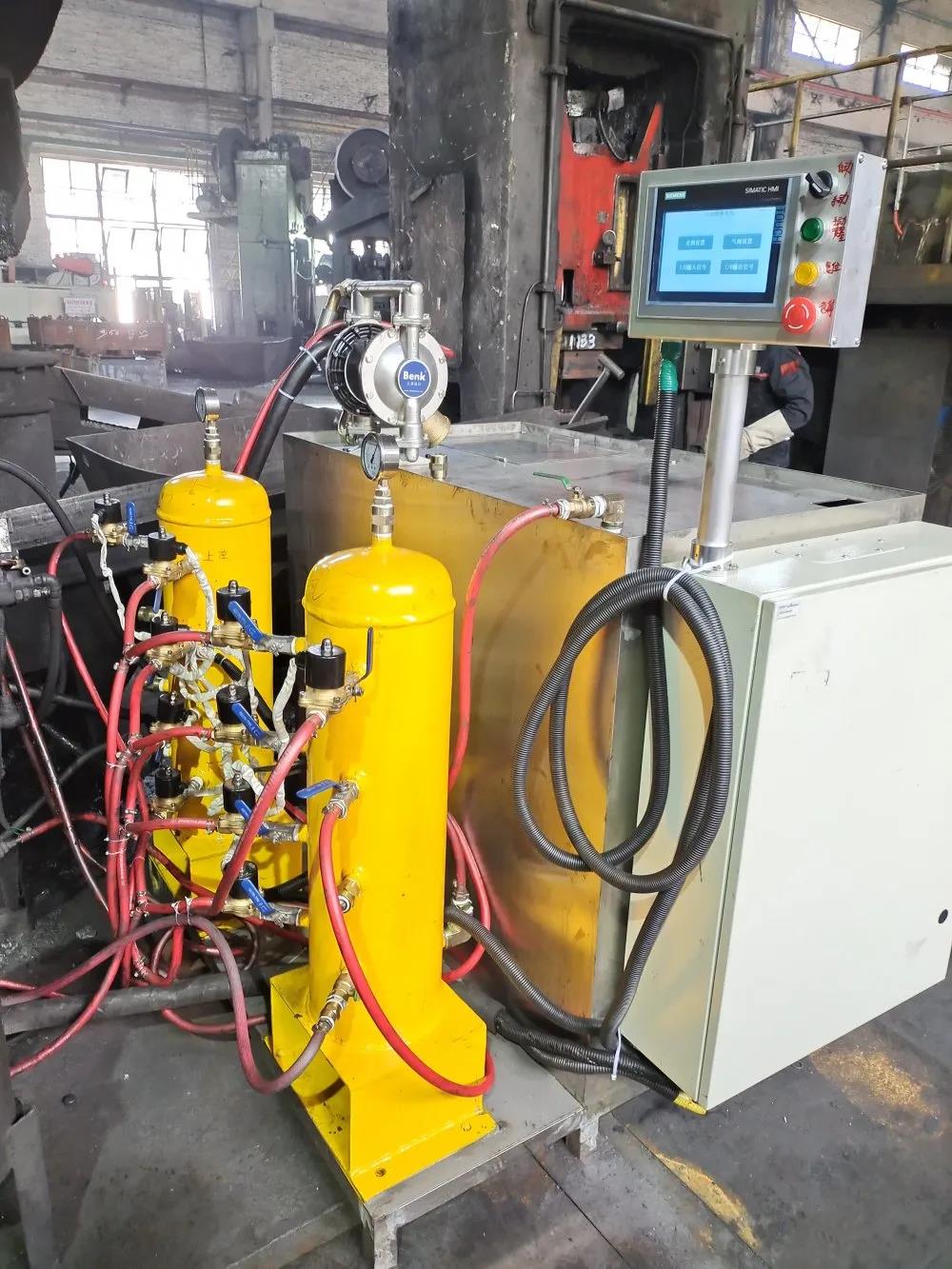
“自动喷墨润滑机的使用能够明显降低工人操作强度、提升工作效率。”锻造厂产品研发科副科长张绍忠介绍,在未采用自动喷墨设备之前,需要2位操作工相互配合进行生产,往往会产生锻打与喷墨相互干涉等问题。
为使机器尽快投入使用,工厂技术部门和使用单位开展联合攻关,解决设备在安装调试中可能遇到的问题。
针对具体困难,大家快速聚集在一起进行头脑风暴,经过仔细观察和讨论,仅用一个白班时间完成安装调试。
随着锻造厂第一台自动喷墨润滑机成功投入生产,工厂在实现技术降本增效的道路上又前进了一大步:操作人员减少到1人,锻打效率提升25%,未来,班产量有望由2500件突破到4000件。
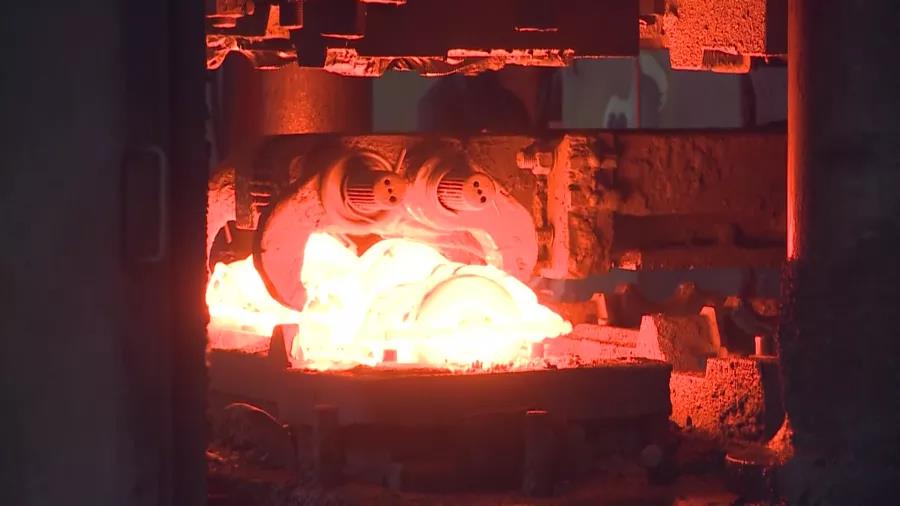
现场改善
“员工每天在这样的快节奏下生产,我们一定要想方设法提升效率,哪怕只是1分钟,我们都应该努力争取。”
5月,东风商用车车辆工厂全力突破单日818辆产量大关,向建厂以来最高产量发起冲锋,工厂辊压二车间主任张会彬介绍,在迈向最高产量的过程中,生产现场也遇到了许多前所未有的难题。
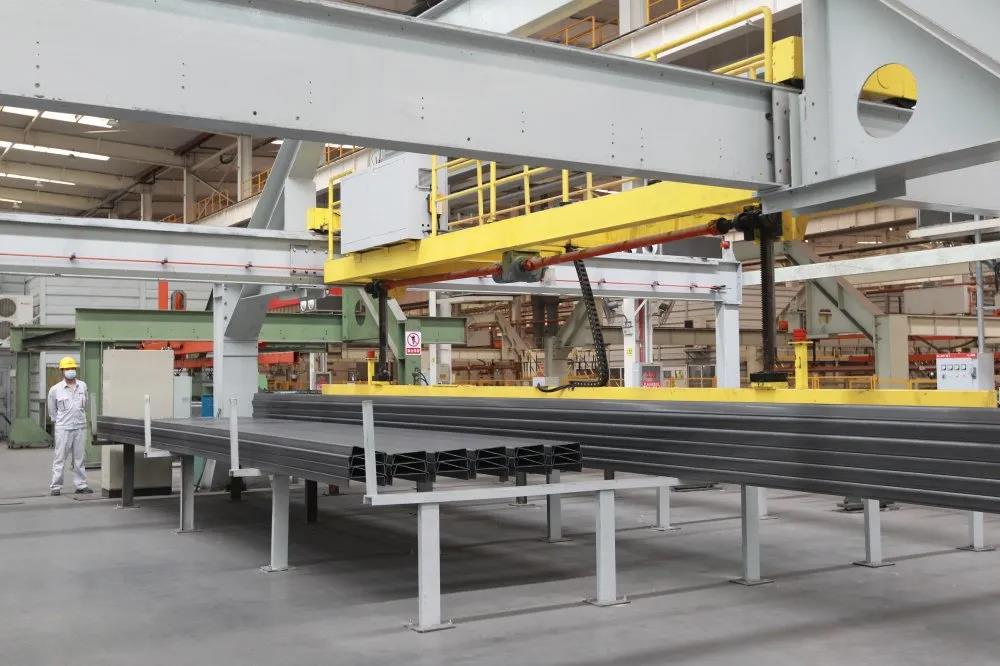
“关爱员工就是要想方设法解决员工遇到的实际困难。”站在数控等离子切割机前介绍改善成果,张会彬语气坚定。最近,他与同事们共同完成的这项改善解决了困扰整个车间12年的难题。
辊压二车间数控等离子切割工序是依据产品外形需求,利用机器手臂对纵梁进行外形切割作业。“示教”主要是为了满足产品的加工尺寸设置机器手臂的运动轨迹,通俗来说,就是依据工艺参数,让机器手臂在零件上模拟走一遍。
但这一“示教”调整频次高、时间长,工作效率很低。为解决这一困难,副厂长戴文海率队开展调研,要求全力解决这一瓶颈问题。
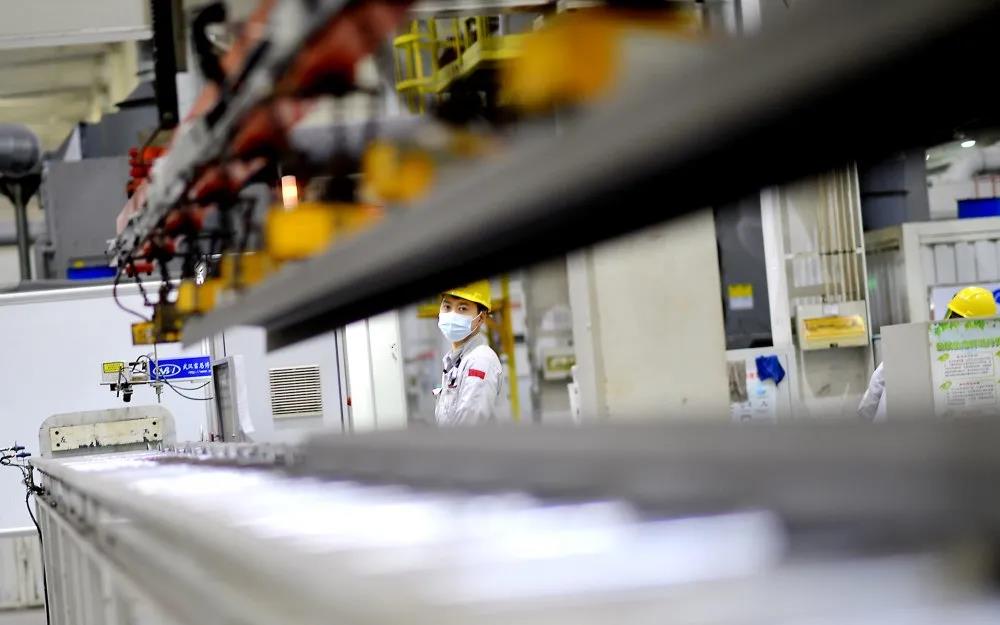
经过改善团队日夜奋战,终于使切割程序与生产计划同步。“这意味着切割机程序以后可以免示教了。”张会彬介绍说,这也为车间产能提升带来巨大空间。
“我们要聚焦现场解决实际问题,从主动改善做起,通过技术手段,降低员工的劳动强度。” 这是东风德纳车桥有限公司制造工程部齿轮研究所所长李琼,在部门视频例会上就解决热处理产能问题提出的要求。
据了解,东风德纳车桥十堰工厂5月、6月齿轮链生产计划分别为6.5万套和6.2万套,再创历史新高。而工厂热处理车间现有8条渗碳炉生产线,月度最大产能为5.99万套,产能缺口显而易见。
为此,齿轮研究所热处理工艺室协同车间,广泛调研排产现状,认真分析产品分类情况,制定出一系列提高产能的工艺方法。
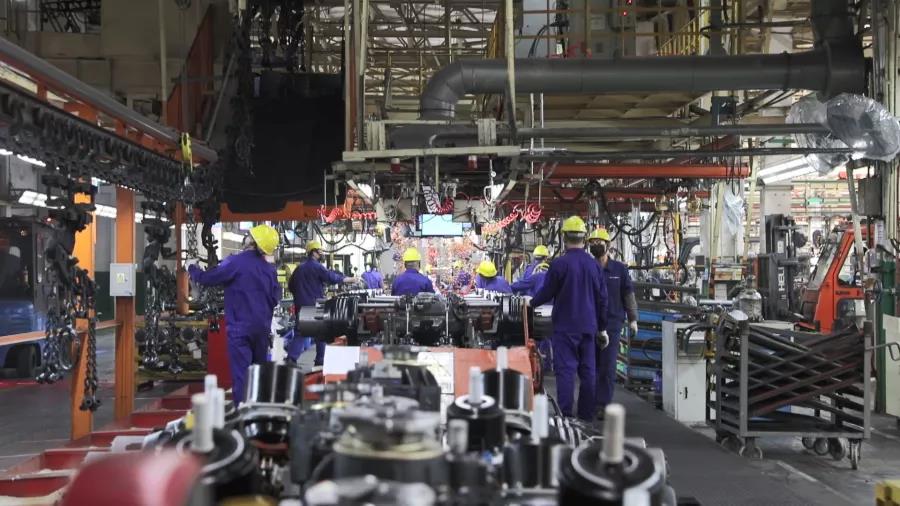
在多部门的共同努力下,通过优化机床动作与工艺参数,改进工装等手段,440大轮装载量由5件/盘提升到6件/盘,推料周期从25分钟/盘降低到22.5分钟/盘,JPH提升33.3%;457、460大轮装载量由6件/盘提升到7件/盘,JPH提升16.8%。
员工是企业的宝贵财富,也是企业实现可持续发展的重要贡献力量, 每一项创新、每一个改善,既是东风商用车对智能制造的孜孜以求,更是其注重人性化管理的具体实践
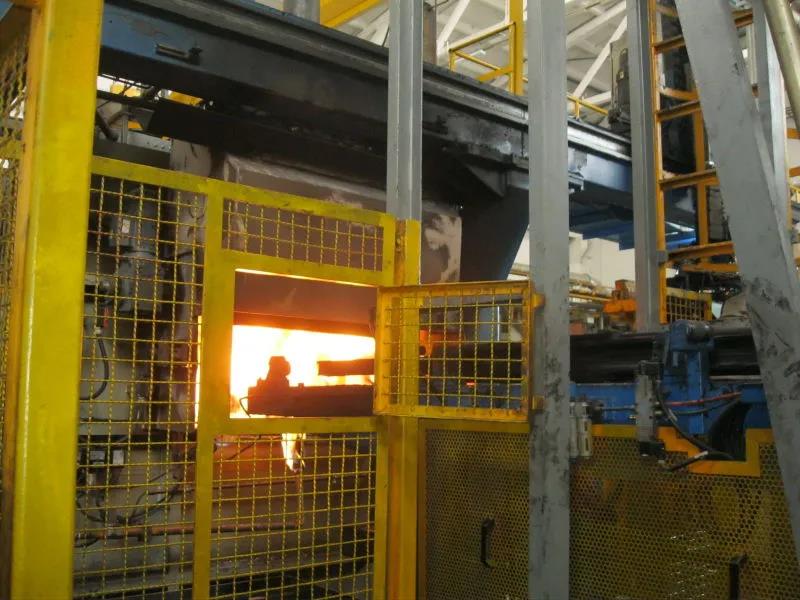
资 讯 快 报
东风商用车实现杭州OBD在线接入排放动态监管,为减少重型柴油车带来的空气污染问题,同时应对各省环保要求,东风商用车积极应对,为打赢蓝天保卫战而努力。前期,东风商用车制定了“1+5+3”和“T+60”快速应对机制,目前已实现车辆快捷接入监管平台,在杭州地区累计接入东风商用车1976辆。东风卡友可通过登录支付宝、浙里办、微信,使用“便民车检”、机动车排放检验等进行查询。
东风新疆在山东、新疆、河南等地举办商品推介会, 近日,东风商用车新疆有限公司在山东临沂、新疆乌鲁木齐、河南洛阳等地举办产品推介会,把产品开到客户“家门口”,邀约客户零距离体验车辆,现场累计发掘意向订单42辆,签订购车合同18辆。